「佐渡島の金山」では西三川砂金山、相川鶴子金銀山の2つの異なるタイプの鉱床に適した技術で採掘が行われ、それぞれ砂金や鉱石を得ていました。
西三川では「大流し」と呼ばれる砂金採掘法で砂金を採取し、採れた砂金は全て相川の奉行所へ送られていました。
ここでは相川で行われていた鉱石の採掘から小判ができるまでの工程を紹介します。
江戸時代の鉱山技術
1鉱石を掘り出す(採鉱)
鉱石を掘り出す方法は、初期の段階においては、地表面に露出している鉱脈をまわりの土石ごと掘りとる「露頭掘り」が主体でした。佐渡金銀山のシンボル「道遊の割戸」も露頭掘りの代表的な例です。
露頭掘りは、地表近くから比較的容易に鉱石を掘り取ることができる反面、鉱脈を追って深く掘り下げていくと鉱石の運び出しや排水が難しくなります。そのため、地下深くにある鉱脈を掘るために「坑道掘り」という技法が用いられるようになりました。坑道掘りは山の横から鉱脈をめがけてトンネル(坑道)を掘ることで、排水と鉱石の運搬がしやすくなり、複数の鉱脈を同時に掘り進めることができるという利点がありました。
坑道を水平に掘るため、高度な測量技術が発達しました。また、坑道が深くなると湧き水が問題になりますが、湧き水を効率的に排水する道具である水上輪(すいしょうりん)が導入されたほか、木材を組み合わせて、坑道内の弱い部分を補強する山留(やまどめ)技術が発達しました。
鉱石は、金穿大工(かなほりだいく)が鑽(たがね)という採掘用の「のみ」を上田箸(うえだばし)ではさみ、鎚(つち)で打って掘りました。上田箸ではさむことで短くなった鑽も使用できました。相川金銀山の鉱石はとても硬く、1日に10㎝位しか掘れなかったといわれています。また、金穿大工1人当たり、鑽を2日で1本消費したといわれています。坑道の換気には、穀物の選別作業で使用する唐箕(とうみ)を改良して使用していました。
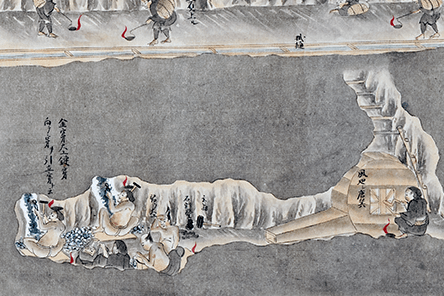
(『佐渡国金銀山敷岡稼方図』新潟県立歴史博物館所蔵)
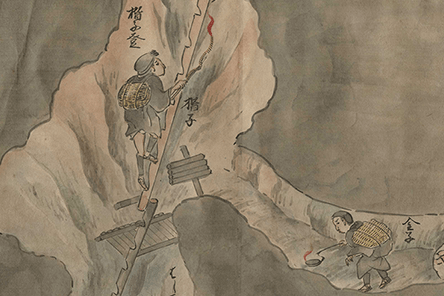
(『佐渡の国金掘ノ巻』相川郷土博物館所蔵)
排水技術
坑内での採掘は常に水との戦いであり、排水は坑内労働の中で最も重要な作業でした。古くは「つるべ」やスポイトの原理を利用した「寸法樋(すぽんどい)」が利用されていましたが、1653(承応2)年に「水上輪(すいしょうりん)」が導入され、排水が効率的に行われるようになりました。
水上輪は筒の内部に螺旋状の板を取り付け、筒が回転することにより、水を汲み上げる排水具で、いわゆるアルキメデス・ポンプとして西洋でも古くから利用されており、中国を経て江戸時代に日本に伝わりました。
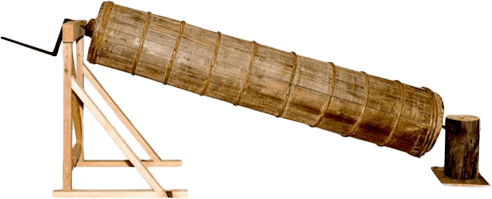

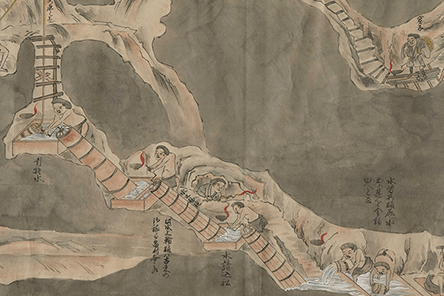
(『佐渡の国金掘ノ巻』相川郷土博物館所蔵)
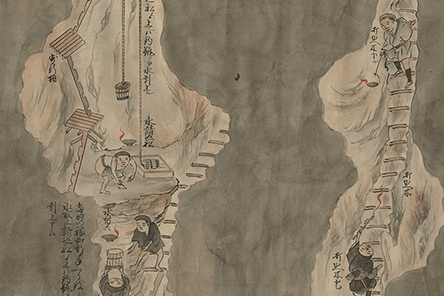
(『佐渡の国金掘ノ巻』相川郷土博物館所蔵)
2鉱石を選別する(選鉱)
掘り出されて品質ごとに仕分けられた鉱石は勝場(せりば)に運び込まれ、鉄のハンマーで砕かれたのち、石臼でさらに細かくすりつぶして砂状にされます。これを水槽に入れてゆり板でゆすり、軽い砂と重い金銀分に分けて回収します。残った砂には、まだわずかに金銀が含まれているため「ねこ流し」という工程にかけられます。水の流れているすべり台のような形の木の枠に木綿の布を敷き、その上に砂状の鉱石を流し、木綿の布に付着した金銀を回収する作業を何度も繰り返しました。
佐渡で鉱石を砕くときに使用されていた石臼は、上臼と下臼の石質を変えて、効率的にすりつぶす工夫がされていました。上臼は吹上海岸石切場で産出する球顆流紋岩(きゅうかりゅうもんがん)を、下臼は片辺・鹿野浦海岸石切場で産出する礫岩(れきがん)が用いられており、それぞれ島内の異なる採石場から石を切り出してつくられました。
金回収の手順
-
01.鉄のハンマーで鉱石を砕く。
-
02.砕いた鉱石を石臼でさらにすりつぶす。
-
03.すりつぶした鉱石を水と一緒に下に引いてある布の上に流して、布に付着した金銀を回収する。(ねこ流し)
製錬
製錬の作業は、床屋(とこや)とよばれる場所で行われました。まず、勝場で回収した金銀と鉛をいっしょに炭火で溶かし、「貴鉛(きえん)」と呼ばれる金銀と鉛の合金をつくります。その貴鉛を灰を敷きつめた鉄鍋で熱すると、鉛が灰にしみ込んで金銀だけが残ります。この作業は「灰吹法(はいふきほう)」といい、石見銀山から伝えられました。次にこの金銀の合金を金と銀に分けるために、硫黄を添加する「硫黄分銀法(いおうぶんぎんほう)」や、塩を用いる「焼金法(やききんほう)」の2つの方法が用いられました。これらを組み合わせ、繰り返すことによって、金の純度は小判の品位(金含有率66~87%)に合わせて高められました。
佐渡奉行所跡から見つかった炉跡や土器などに加え、作業手順を記した技術書や絵巻などの史料類が残っていることで、当時の操業の様子が明らかになりました。焼金法を示す遺構は、世界的にもほとんど残っておらず、国内では佐渡にのみ残っています。また、奉行所の敷地内に選鉱・製錬を行う工場(寄勝場・寄床屋)が設けられている点も大きな特徴の一つです。1759(宝暦9)年、当時の佐渡奉行の石谷清昌(いしがやきよまさ)は、産出量の減少に伴う生産の効率化と、より念入りな工程管理を行うため、相川の鉱山町各所に散在していた勝場や床屋の作業場を奉行所内の工場に集約しました。これにより、奉行所の直接的な管理運営のもと、金生産が行われるようになりました。
製錬の工程
-
01.選鉱工程で得た金銀を含む鉱石の粉に鉛を加え合金(貴鉛)にして不純物を除く。
-
02.鉄鍋に灰を敷き詰め、灰の上に貴鉛をのせて加熱すると、先に鉛が溶けて、灰に染みこみ、金と銀だけが残る。
-
03.灰吹法で得た金と銀の合金を細かく砕く。
-
04.細かく砕いた金と銀の合金に塩を混ぜて円筒形に固める。
-
05.円筒形の塊を土器ではさみ、炉の中に並べ、周囲に炭を充填する。
-
06.長時間加熱し続けると、銀と塩が反応し、塩化銀となって金と分離する。
※写真右写真下:佐渡奉行所の長竈(焼金炉)跡 -
07.焼いた塊を水槽に入れて突き崩すと、塩化銀は水に溶け、金のみが沈殿する。
小判製造
相川金銀山では、鉱石から金銀を生産するだけでなく、小判の製造も行っていました。これは、島という隔絶した地理的条件と、奉行所による一元的な管理体制によって可能となったものでした。鉱石の採掘から小判の製造までを一貫して採掘地(鉱山)で行うのは、世界的にも極めて珍しいことです。小判は奉行所の隣にあった「小判所」で造られました。まず金を溶かし、のべ板状にしたものをハサミで小判1枚分の重さに切り分け、鎚(つち)で叩いて小判の形に成形し、「茣蓙目(ござめ)」という模様を付けます。その後、表面に薬品を塗り、熱を加える「色揚げ(いろあげ)」を行い、より良い「黄金色」にして完成させました。
佐渡の小判は厳重な警護のもと、相川から小木へ、小木から船で対岸の出雲崎へと運ばれ、さらに北国街道から中山道を経て、毎年江戸まで運ばれました。
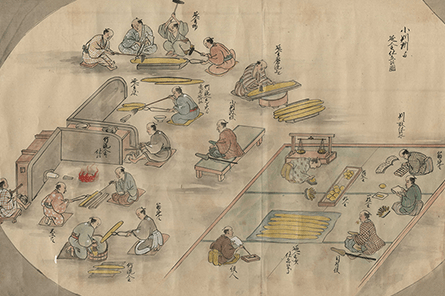
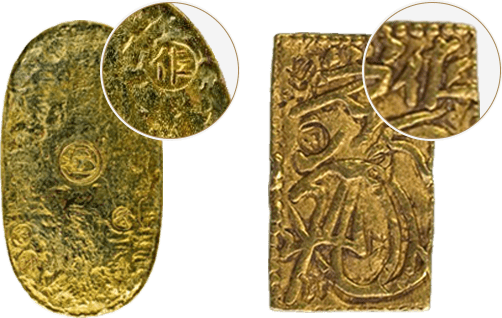